The hard problems behind why the moon landing had to be faked - Part 2: Heat shields
There are great ideas undiscovered, breakthroughs available to those that can remove one of truth’s protective layers.
Orion is the crewed portion of the Artemis spacecraft that is planned to return man to the moon. An un-crewed module returned to earth on December 11th, 2022 after return from lunar orbit. When the “thermal protective system” (TPS) was examined, significant spalling type damage was found, in excess of that predicted by prior testing and design.
Designing a heat shield for return from lunar orbit is a hard problem. Because the return velocity is roughly 40% faster than from low earth orbit, the heat rates are 666% higher:
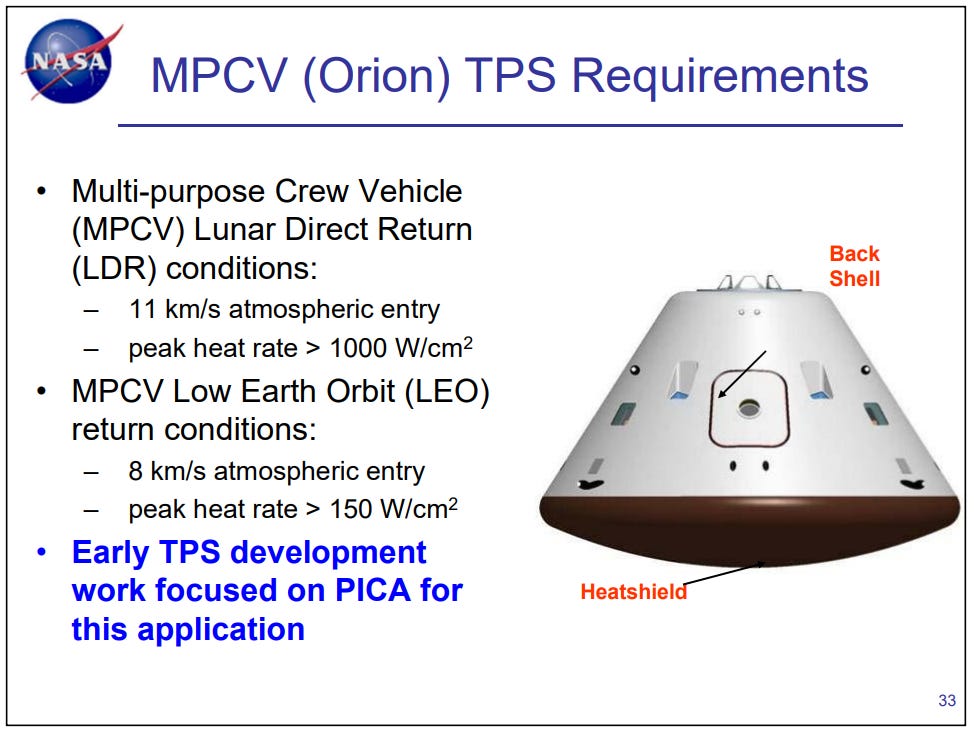
The aerodynamic shape of the spacecraft, and the need to protect humans from loads in excess of 10g, determine the range of possible re-entry profiles. Each profile has different values for three key stats:
Peak heat flux
Heat load
Peak dynamic pressure
Different re-entry profiles result in different heat shield designs:
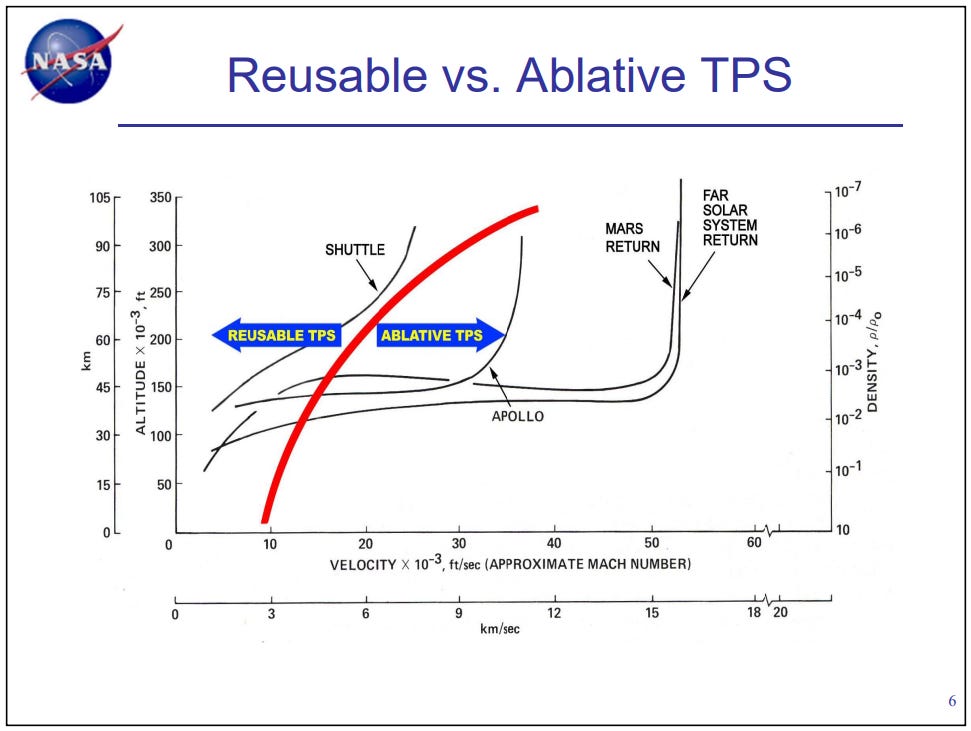
The worst cases are over and undershoot of the re-entry profile. Overshoot lengthens the duration of the re-entry, resulting in higher cumulative heat loads. Undershoot dramatically increases the peak heat flux and dynamic pressure.
Apollo Command and Service Module
An ablative material called AVCOAT 5026-39/ M is at the heart of both the Apollo CSM and Orion heat shields. It works by generating char through a process called pyrolysis, which blows gas everywhere - slowing convective heat transfer. It is intended to be consumed but in a controlled manner. One failure mode is spallation - chunks blowing off. The spallation failure mode occurs in response to high pressures and heat fluxes - the undershoot design case.
AVCOAT was developed by AVCO (later Textron) in partnership with the Langley Research Center. A severe testing program took place after Apollo and used the following equipment, each of which simulated different combinations of the three key stats (peak heat flux, heat load and peak dynamic pressure):
Langley 20-inch hypersonic arc-heated tunnel:
Langley ll-inch hypersonic ceramic-heated tunnel:
Arc-heated materials jet
The introduction of the report includes the following statement:
Recently, however, ground- and flight-test results have indicated that the material ablates at unexpectedly high rates when exposed to severe reentry environments which produce high pressures (higher than those expected during an Apollo reentry) on the char surface.
“Flight-test results” - An earlier flight test with a scale model intended to simulate the undershoot case resulted in complete erosion of the AVCOAT heat shield. More on this later.
In an attempt to achieve an improved understanding of the ablation behavior of this material, a series of studies were carried out in three high-enthalpy wind tunnels at the Langley Research Center on a molded ablator which had the same composition as the Apollo material but which was not fabricated with a honeycomb matrix.
Enthalpy is the total heat content of a system, taking into account its pressure and volume. High heat flux and high pressures generate high enthalpy conditions.
One of their key findings was that when the AVCOAT failed in high enthalpy conditions (the undershoot case), it failed quick:
At high values of Ho (that is, high values of heating rate and pressure), the ablation rate of the material increased rapidly with increasing heat-transfer coefficient and severe mechanical char failure was observed.
Back to the scale tests using two foot models. The first was called FIRE I, and was conducted in 1964. It was not intended to simulate over or undershoot. Instead, its purpose was to confirm the thermal predictions and design methods. It succeeded, producing data right in the middle of the error bars:
The second scale model test was called R-4 and was launched later in 1964. This one was intended to simulate the 20g undershoot case.
To match the Apollo heating rates at less than lunar-return entry velocity, the fifth stage of the Scout vehicle was ignited late in the entry phase into the earth atmosphere, so that high heating rates occurred at a lower altitude.
This test was less successful:
The telemetered ablation-rate data from this flight indicated that the rates encountered were much higher than had been expected, particularly during the later stages of entry, and, in fact, resulted in complete erosion of the 1.25-inch-thick ablative material.
Management was not pleased:
There was much consternation as a result of these findings, and considerable analyses and testing were done to convince the Apollo Program management that the poor performance of the R-4 test spacecraft was a characteristic of the Avco 5026-39 ablator at high aerodynamic pressures, but that the high pressures encountered in the R-4 test were not representative of the Apollo entry environment.
Everyone agreed that the test was too severe:
At the lower altitude, the heating rates approximated those an Apollo vehicle would experience; however, the resulting freestream dynamic pressures on the Scout vehicle were three times higher than the pressures an Apollo CM would undergo on entry into the earth atmosphere.
The next step was full-scale tests of unmanned craft. The maximum heating rate tested was 425 Btu/ft^2. Much lower than 1000 Btu/ft^2 for the successful FIRE 1 scale test.
The following graph shows a comparison between the manned Apollo flights and the AS-501 and AS-502 tests. The R-4 with its completely eroded shield is somewhere past the 20g undershoot curve.
All the Apollo flights are tucked in the safe part of the operating region. The heat shields (TPS) look great afterwards:
“There comes a point in every project when you have to shoot the engineers and put the product into production”.
What was all the consternation about? Mission accomplished right?
Unmanned Missions
Unmanned missions do not have the design constraint of a 10g maximum on their re-entry profile, or the temperature constraints of not barbequing humans, and can therefore use different TPS designs.
Luna 16 returned samples from the moon in 1970.
The heat shield was a pure sphere design. Below is the return stage in a field somewhere.
NASA’s Genesis probe didn’t visit the moon, instead in 2001 it traveled beyond it to collect solar wind samples. It crashed because its parachute failed but it appears the heat shield worked great.
The heat shield is made of a graphite-epoxy composite covered with a thermal protection system. The outermost thermal protection layer is made of carbon-carbon. The capsule heat shield remains attached to the capsule throughout descent and serves as a protective cover for the sample canister at touchdown. The heat shield is designed to remove more than 99 percent of the initial kinetic energy of the sample return capsule.
China’s Chang’e 6 returned samples from the far side of the moon in 2024.
Orion heat shield design
The original AVCOAT application on Apollo was a labor intensive process which resulted in a monolithic (one piece) design.
A predecessor to the current Orion design, called the EFT-1, also used the monolithic TPS.
Its re-entry profile peaked at 29,000 fps, slower than Apollo. Compare its damage to the Apollo 11 heat shield. Despite the slower speeds, it looks worse:
For Orion, NASA decided to switch things up and move to a tile-based construction, for ease of manufacturing. This despite the fact that Orion was planned to do a full speed re-entry, like Apollo, at roughly 36,700 fps.
Orion also will be the first manned spacecraft to use the “skip re-entry”. China’s unmanned Chang'e 6 also used this technique. It involves intentionally flying near the overshoot case. The design tradeoff is more cumulative heat load, but less peak heat flux and dynamic pressure. Basically, staying even farther away from the high enthalpy conditions of the undershoot case, which generate spallation damage.
Which brings us back to the damaged Orion heat shield from 2022.
NASA studied the Orion heat shield problem for two years, and in 2024, its Inspector General released a report giving the project a clean bill of health for a manned mission.
Something just doesn’t add up. The scale and unmanned flight tests that preceded Apollo pushed the performance boundary far beyond that of the manned flights. There’s a long history of successful development for unmanned craft with similar technology. Yet the Apollo re-entry can’t be replicated with Orion, despite flying a skip profile that avoids the high enthalpy conditions previously associated with spallation damage.
Do you believe this is real:
Or do you believe that the consternation the engineers felt 58 years ago was real and that the program would be best served by picking up where they left off - with scale models?
Part three is about big boosters:
The hard problems behind why the moon landing had to be faked - Part 3: Big boosters
President Kennedy: Do you think the lunar, the manned landing on the moon is a good idea?
If I understand it correctly, the new TPS for the Artemis/Orion project, based on the old Apollo technology (and supposedly improved), is unable to reach the performance needed for a high energy re entry like a return from Luna. Although the TPS worked 100% of the time in the Apollo missions.
You found the origin of the Star Trek insignia